Add Plastic Regions
If an RS3 model incorporates a nonlinear material, a plastic analysis to the whole model will be conducted to ensure that the stress state remains within the specified yield surface of the material.
The Add Plastic Regions option enables you to designate specific regions in the model to undergo plasticity analysis. This feature is useful when you have a particular area to focus within the complex model, and would like to allocate the computation resource to that specific area for plasticity analysis. For example, you can add a plastic region to a known highly unstable area, in order that plasticity analysis will only be performed within that area while maintaining the rest of the region elastic. This approach aids in reducing the computation time.
- The Add Plastic Regions option has the OPPOSITE functionality to the Exclude Plastic Regions
option.
- This option is only available to plastic materials. See the How does the Add Plastic Regions work? section below for details.
- Plastic region and exclude plastic region can be added in the same model, while they must intersect with each other. See the Different Regions section below for details.
- This feature is applicable for joint and liners that are inside the plastic region.
When a plastic region is defined, materials within that region retain their plastic behavior, while all materials outside of the region are set to behave elastically. Hence, plasticity analysis will only be performed within the defined plastic region(s). Below shows a typical case of plastic region application.
Example (case 1)
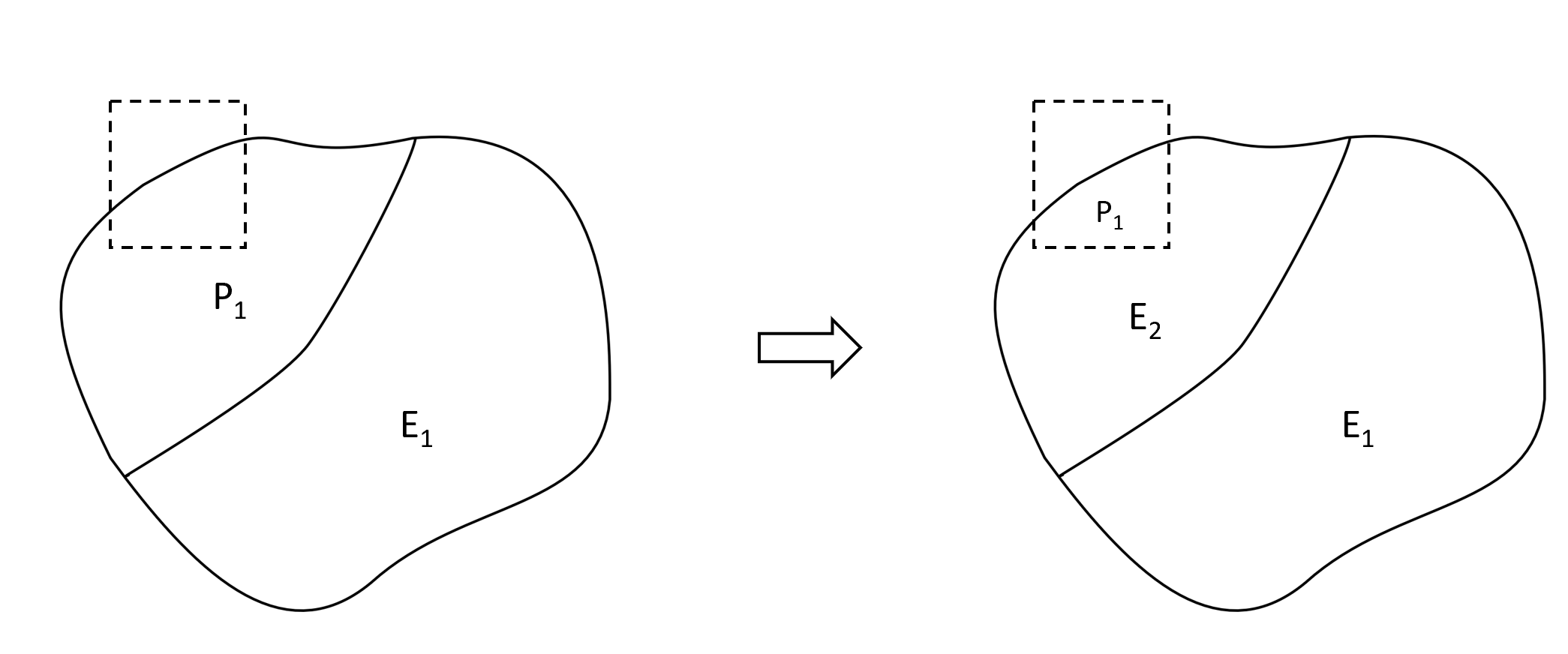
As seen in Figure 1, to start with, the model contains two material types, plastic (P1) and elastic (E1). A plastic region (dashed box) is added to the top left corner of plastic part. The area within the box remains plastic (P1), the area outside the box that was initially plastic is switched to elastic (E2), and the area outside the box that was initial elastic remain elastic (E1).
Steps
Two methods are provided to define a plastic region: a) by creating a box, and b) by setting a volume. Both methods are described below.
- Ensure the material properties have been defined with the Define Material Properties option from the toolbar or the Materials menu. Ensure Material Type = Plastic under the Strength tab.
- Create a Box
- Select the Add Plastic Region
option from the Materials menu. You will be prompted to a dialog.
- The plastic region dimension can be defined using either: the Create Plastic Region dialog, or the Freehand Manipulation tool
.
From the Create Plastic Region dialog, choose a box dimension definition method from the dropdown list.
- If Defined By = 2 Corners, the XYZ coordinates for the two corner vertices of the box need to be specified.
If Defined By = Dimensions, the XYZ coordinates for the center point of the box, as well as the length, width, and height dimensions of the box need to be specified.
The expandable Rotation Angles section can rotate the box. The rotation angles around the X, Y, and Z axes are required.
- A Freehand Manipulation tool
will appear in the viewport. It is placed at the center of the box by default. You can hover the mouse to place the tool at any corner. When the Freehand Manipulator is at the center, you can drag the tool to translate the box, or drag the curve to rotate the box. When the tool is at a corner, you can drag the arrow to resize the box dimension along the corresponded axis.
- The dimension and rotation angle will be updated in the Create Plastic Region dialog.
Under the Create Plastic Region dialog, the Reset (N) button can reset the box to its original form. The Cancel button can close the dialog disregarding all changes made.
When completed, select OK to apply and exit the dialog. The plastic region will be added to the model and under the Visibility Tree as an entity named "Plastic Region".
To edit the region, you can use the Editbutton from the Properties pane. See the Edit Plastic/Plastic Exclude Regions for details.
- Now, the area within the defined region will be plastic, and the rest of the model will be elastic.
- Continue to step 5 below.
- Set a Volume
- Select a volume entity either from the Visibility Tree, or from the model with the Entity Selection tool
from the toolbar.
- Select the Add Plastic Regions
option from the Materials menu.
The selected volume is now set as a plastic region. An entity named “Plastic Region” will be added under the Visibility Tree.
- Now, the area within the defined region will be plastic, and the rest of the model will be elastic.
- Now, the area within the defined region will be plastic, and the rest of the model will be elastic.
- Repeat step 2-4 to add more plastic regions. For more examples about single, multiple, or different regions, see the section below.
- When Completed, proceed to finish your model, apply Mesh and Restraints, and Compute.
- After Compute, you can view the RS3 compute file to see the material type changes due to plastic regions.
How does the Add Plastic Regions work?
As mentioned, the Add Plastic Regions option is only available for plastic materials. Its typical use is as shown in the example above (see Figure 1).
Below shows the scenarios when elastic materials are involved. Single and multiple plastic regions, as well as different regions are presented.
Single Plastic Region
Case 2
Figure 2 below presents a case in which a part of elastic material included in the plastic region, represented by a dashed box. In this case, the included elastic material will remain elastic, and the elastic material outside stays elastic as well. No change will be applied to the model.
When hitting Compute, a message will pop up: “The plastic regions do not affect the model.”
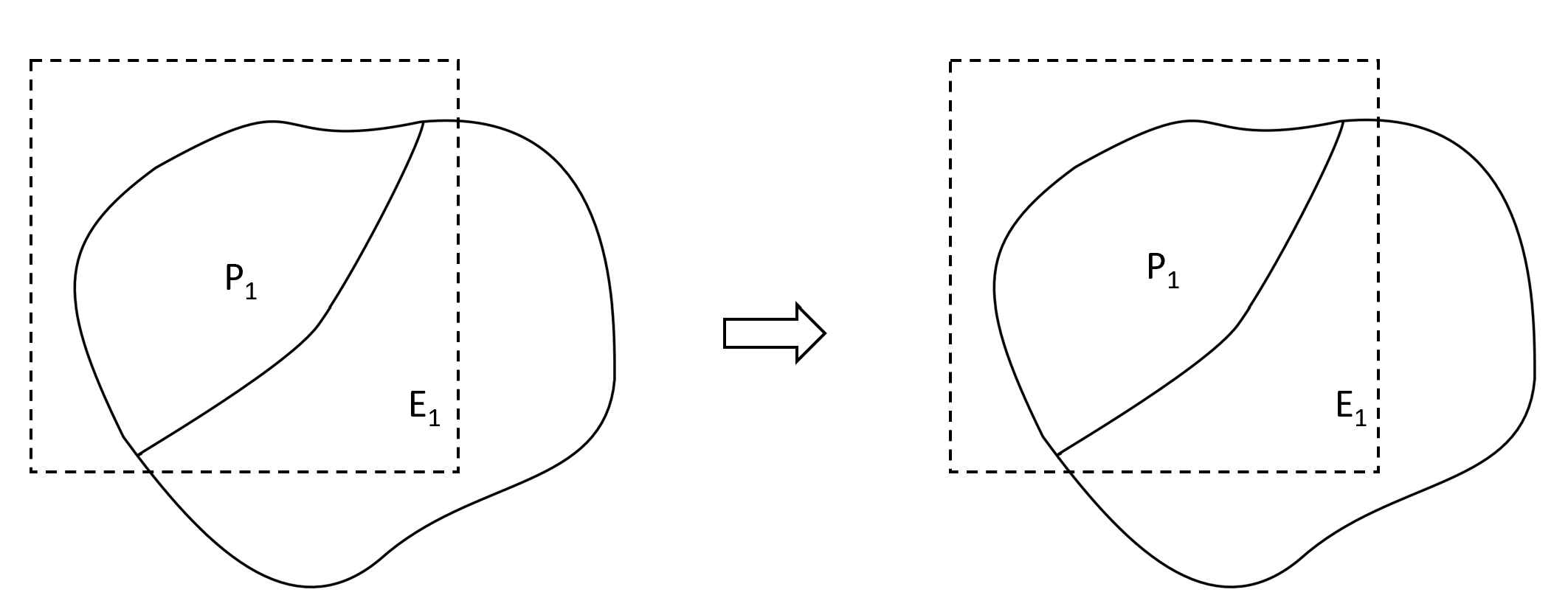
Case 3
Figure 3 below shows when only elastic material is included in the plastic region, represented by a dashed box. In this case, no change will occur inside the region, while the plastic material outside (P1) will be switched to elastic (E2).
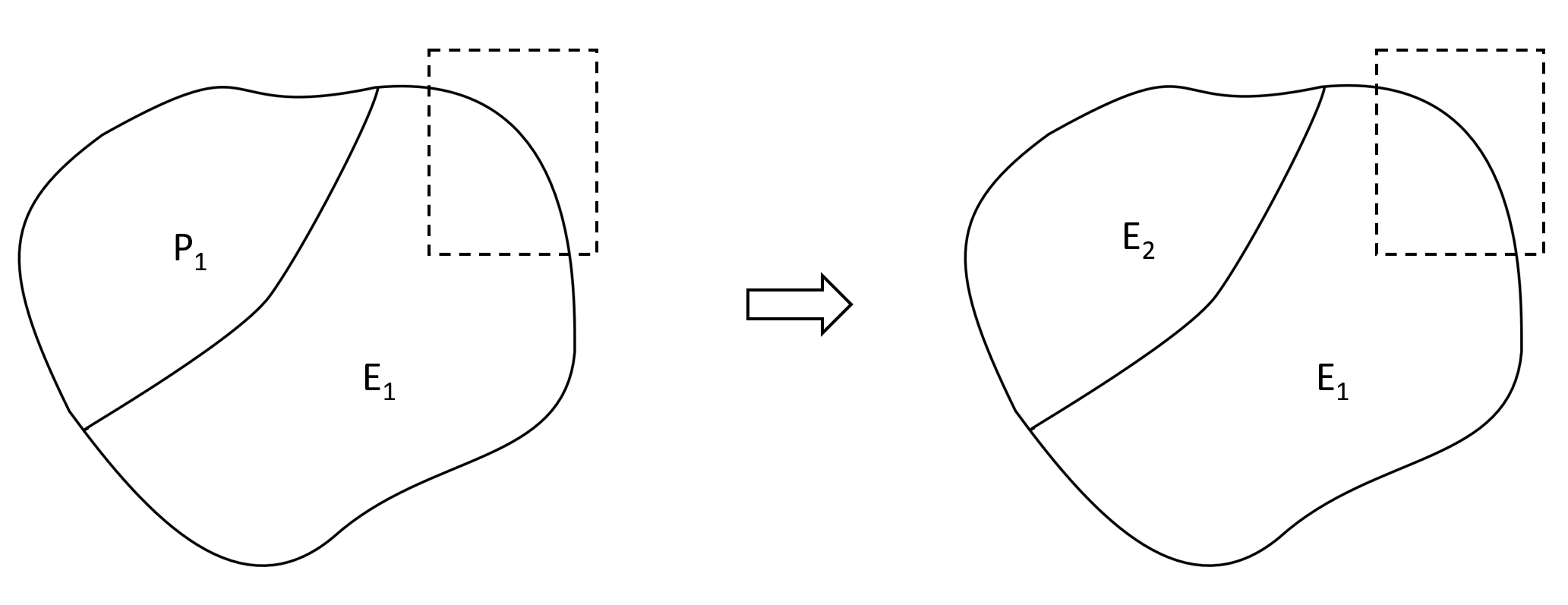
Case 4
As shown in Figure 4 below, an addition of a plastic region within a model that solely consists of elastic material is not applicable. This action will not make any changes to the original material behavior.
When hitting Compute, a message will pop up: “The plastic regions do not affect the model.”
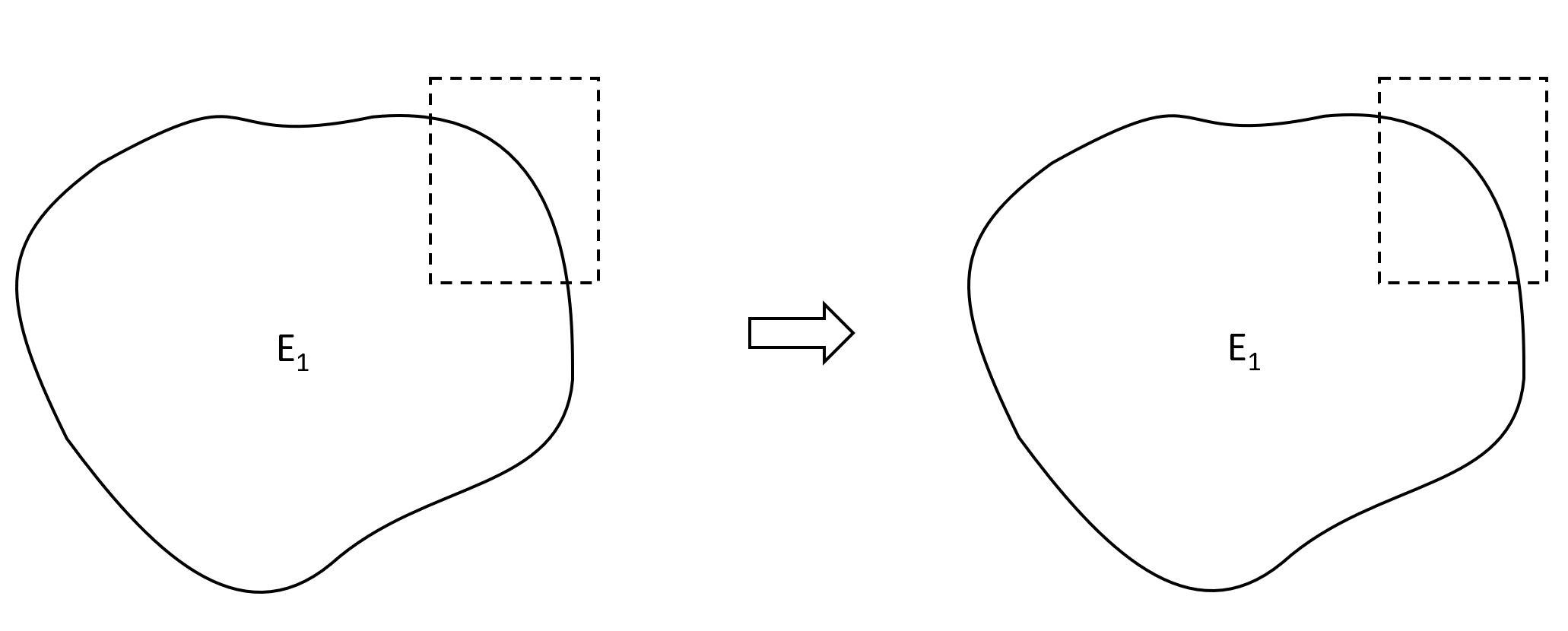
Multiple Plastic Regions
Case 5
Multiple plastic regions are supported in RS3. As seen in Figure 5 below, two plastic regions are added to the model. The plastic material inside the two regions remains plastic (P1), while the remaining portion becomes elastic material (E2). The presence of plastic region casts no impact on the elastic material (E1).
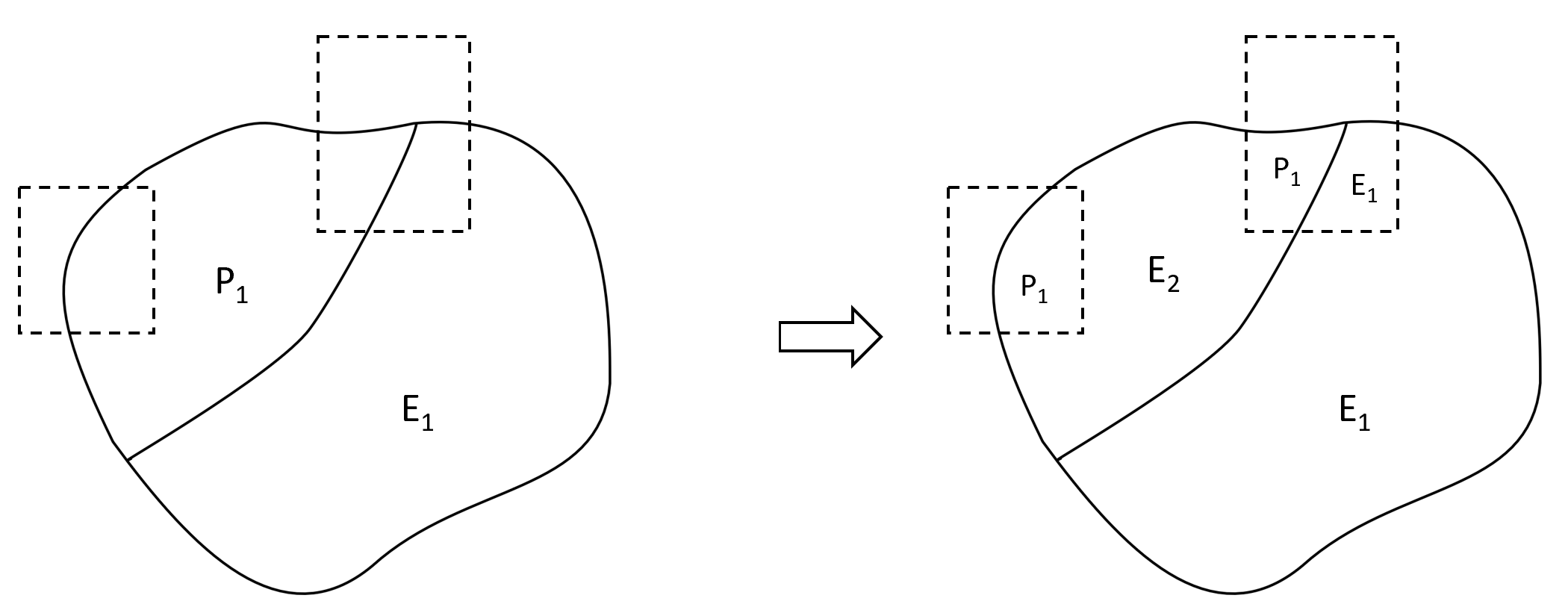
Different Regions
Add / Exclude plastic regions can be applied in the same model at the same time. Two cases are shown below.
- Each region must intersect with a region of the other type. Otherwise, it is not applicable (see Figure 6).
- The material type of intersected regions is governed by the final layer of the Add /Exclude plastic regions that is applied to it (see Figure 7).
Case 1
Figure 6 shows an invalid example, where two different regions do not intersect. The black dashed box represents a plastic region, and the blue dashed box represents an exclude plastic region. In such cases, a warning message will display: “New region needs to intersect a plastic / exclude plastic region.”
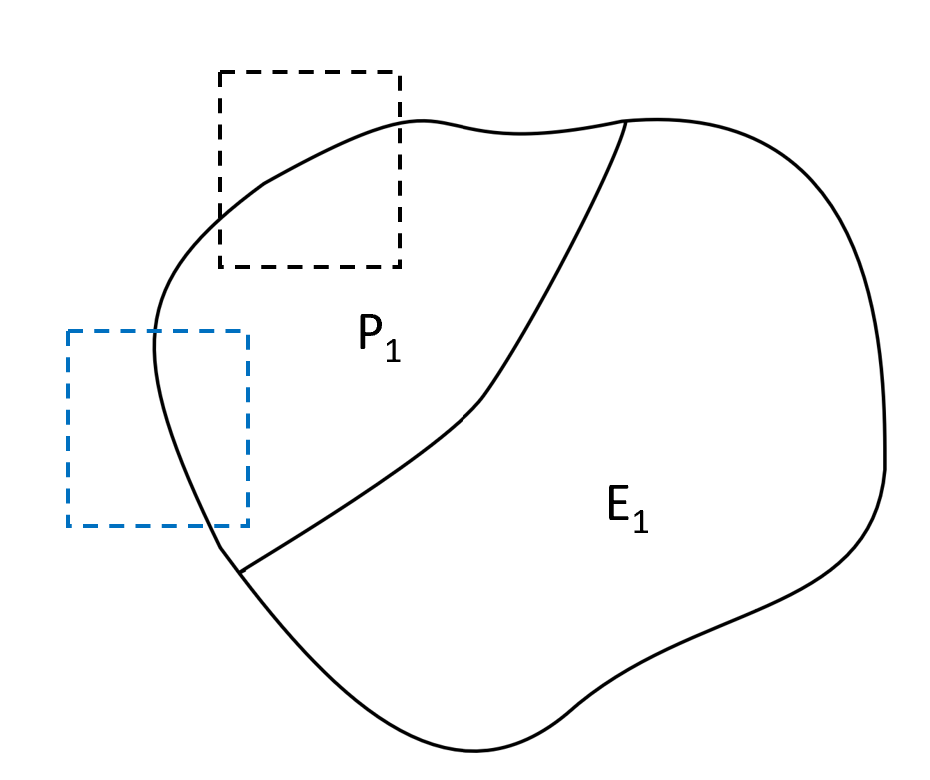
Case 2
Figure 7 below shows a valid example. A plastic region is added FIRST (black dashed box), and an exclude plastic region (blue dashed box) is added AFTER. An intersected area is included.
The plastic material within the plastic region remains plastic (P1) and the plastic material outside this region is switched to elastic (E2). The plastic material within the exclude plastic region is switched to elastic (E2). To be mentioned, the intersecting area (shaded) is switched to elastic (E2) – since the exclude plastic region is added the last.
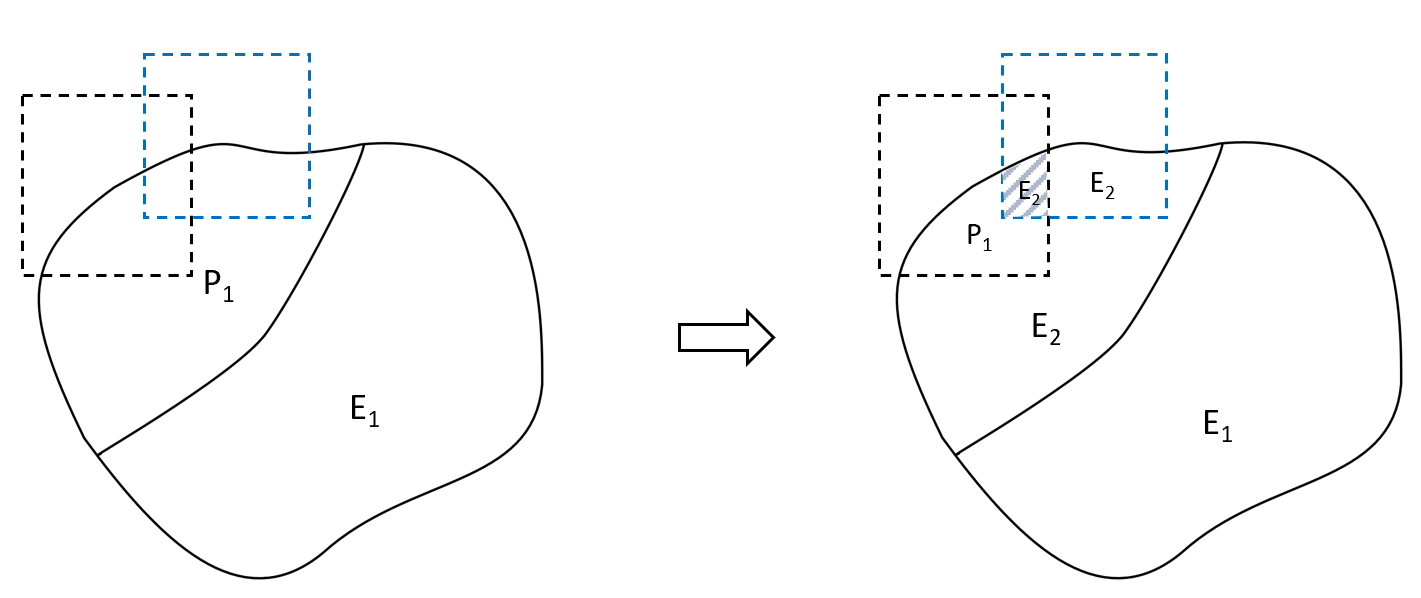
Advanced Constitutive Models
All material models are defined under the Strength tab of the Define Material Properties dialog from the Materials menu. In RS3, the following failure criterions (material models) are categorized as advanced constitutive models, where the strength properties are defined without specifying a plastic/elastic material type:
- Elastic/Plastic
- Discrete Function
- Softening/Hardening
- CamClay
- Modified CamClay
- MC with Cap
- Softening-Hardening Model
- Barcelona Basic
- NorSand
- Dynamic
- Bounding Surface Plasticity
- Manzari_and_Dafalias
- Slide Models
- Shear Normal Function
- FLAC
- Ch-Soil
- Cy-Soil
- Double Yield
- PLAXIS
- Hardening Soil
- Hardening Soil with small strain
- Soft Soil
- Soft Soil Creep
- Swelling Rock
For advanced constitutive models,
- when option is ON – materials within the region will remain unchanged, while the materials outside the region will adopt default elastic properties.
- When the option is OFF – the material will remain unchanged. In other words, the material will not be affected by the plastic region.
Generalized Anisotropic Model
Besides advanced constitutive models, the Generalized Anisotropic (GA) model requires specifying the base and joint materials. For plastic regions with GA models:
- within the region, materials will remain unchanged.
- outside the region, GA materials will be assigned its elastic properties with stiffness and Poisson’s ratio, while the base and joint materials will be ignored.