Soil Constitutive Models in RS2
Abstract
The library of material models in RS2 has been expanding, and more constitutive models specifically for soils are now included in the package, for example the Hardening Soil model and Cy-Soil model. On top of built-in constitutive models, RS2 extends its material model library by implementing user-defined dll files. In this article, the Hardening Soil model in RS2 is used in a simulation of a deep excavation in Berlin, Germany, and results are compared to the work presented by Nikolinakou et. al., 2011.
The Hardening Soil and Softening Hardening Models
Major features of the mechanical behavior of soils include plastic deformation or yielding that starts at the early stages of loading, stiffness is proportional to the level of confinement, and volumetric behavior is demonstrated and consists of compaction, followed by a possible dilation under shear loading. Considering these three features, the material models used in the following simulations are taking advantage of a continuous yielding and hardening behavior, a nonlinear elastic behavior in which the Young’s modulus is related to the level of stress, and an appropriate flow rule that can capture compaction and dilation of the volumetric behavior of soils. The Hardening Soil model is used to simulate the behavior of Berlin sand in the following sections.
Site Characteristics
The studied deep excavation is in the M1 pit from the VZB tunneling project in Berlin. The pit was excavated underwater to a depth of 20 meters, and supported by a diaphragm wall.
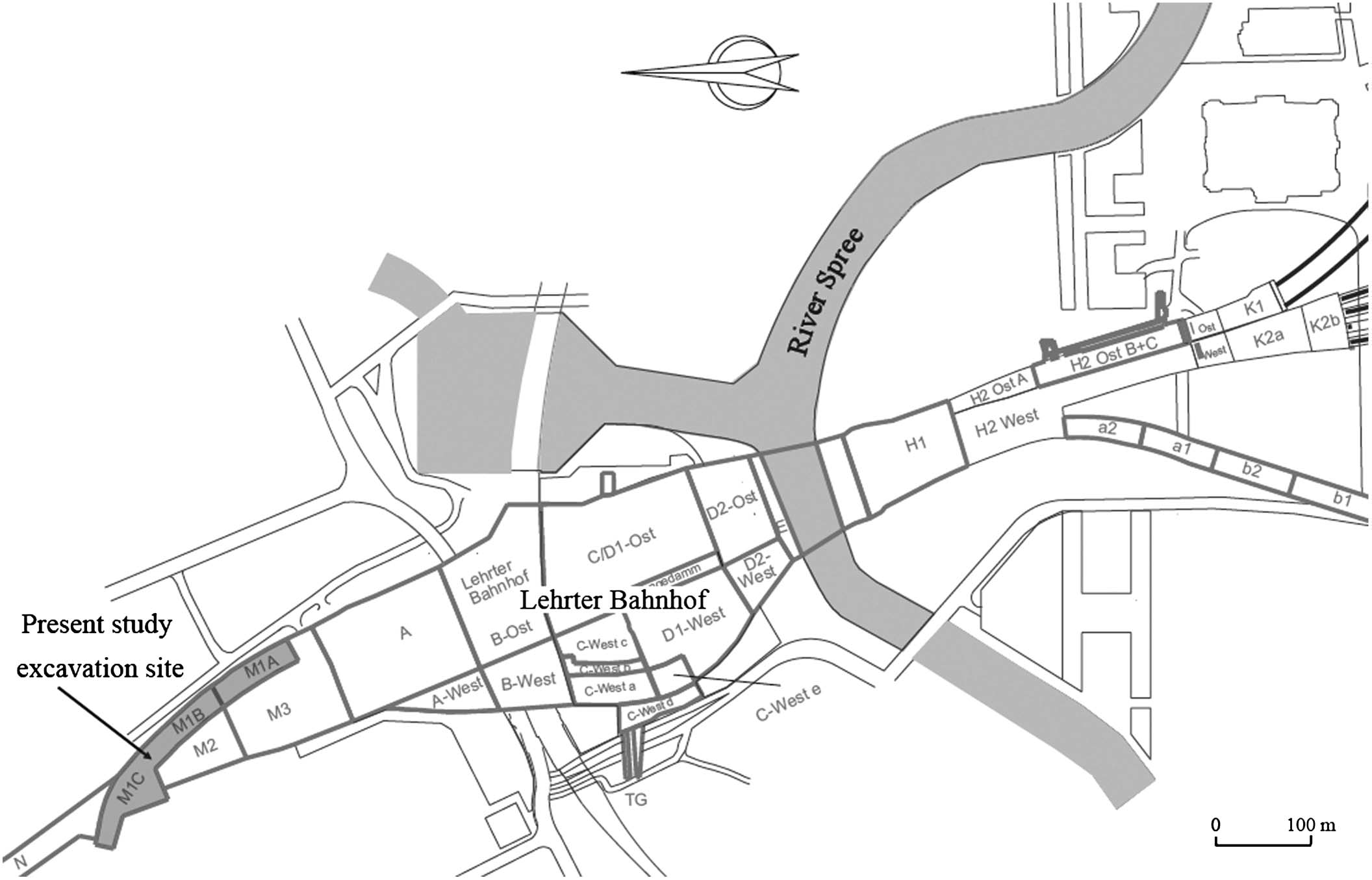
The site soil (Berlin sand) is characterized as saturated glacier deposits from three different deposition periods. Typically, the vertical soil profile consists of one fill layer (3-4m thick) overlying three layers of sandy tilts, including S0 (6m thick with 1-m-thick organic soil), S1 (10m thick), and S2 (below the depth of 22m) (Nikolinakou et. al., 2011).
Model Setup in RS2
This RS2 model includes three primary layers of sand depositions, ignoring secondary fill and organic soil. A 1.5-m-thick diaphragm wall extends to 28.7 meters below the ground soil, and it is supported by a row of pre-tensioned tiebacks. The water table is at 2-m depth, and ponded water pressure is used to model underwater excavation.
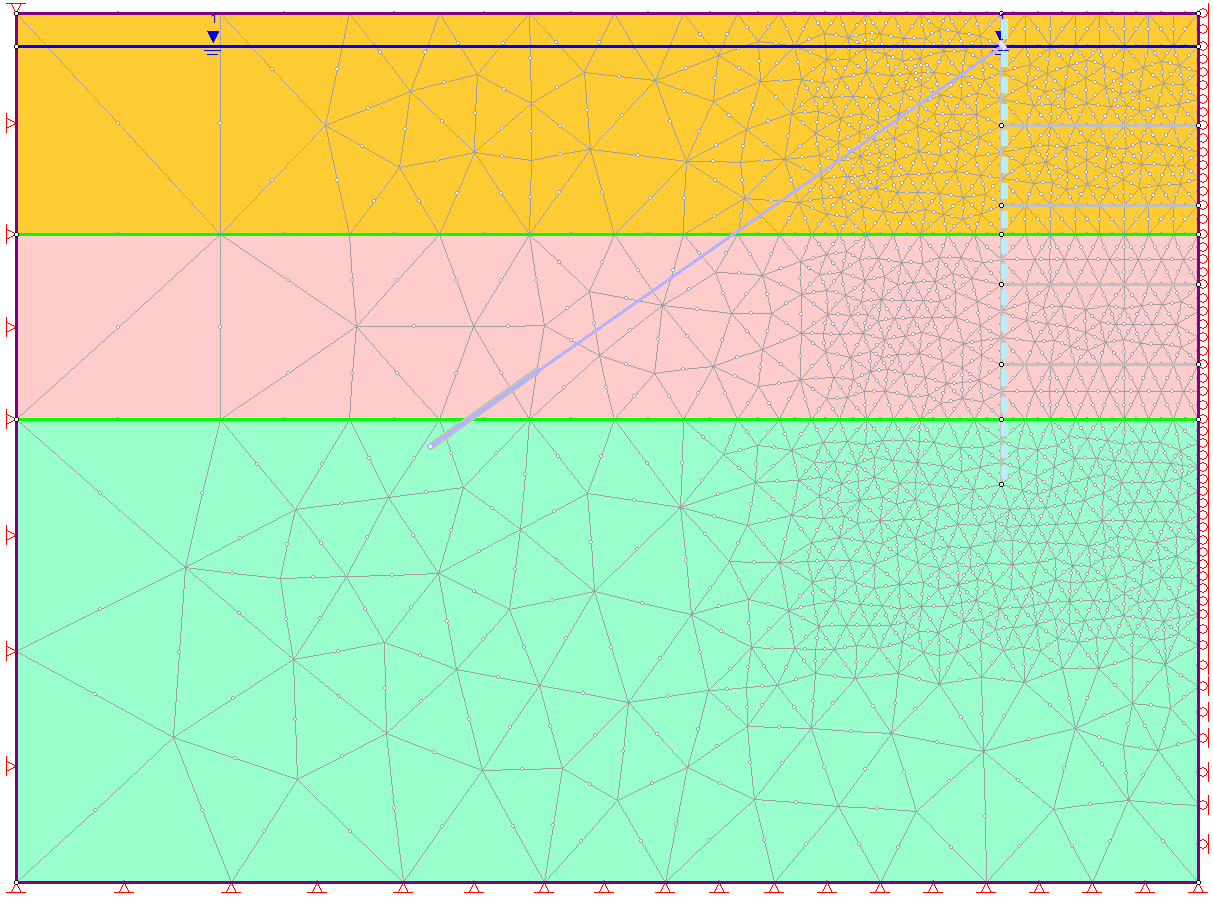
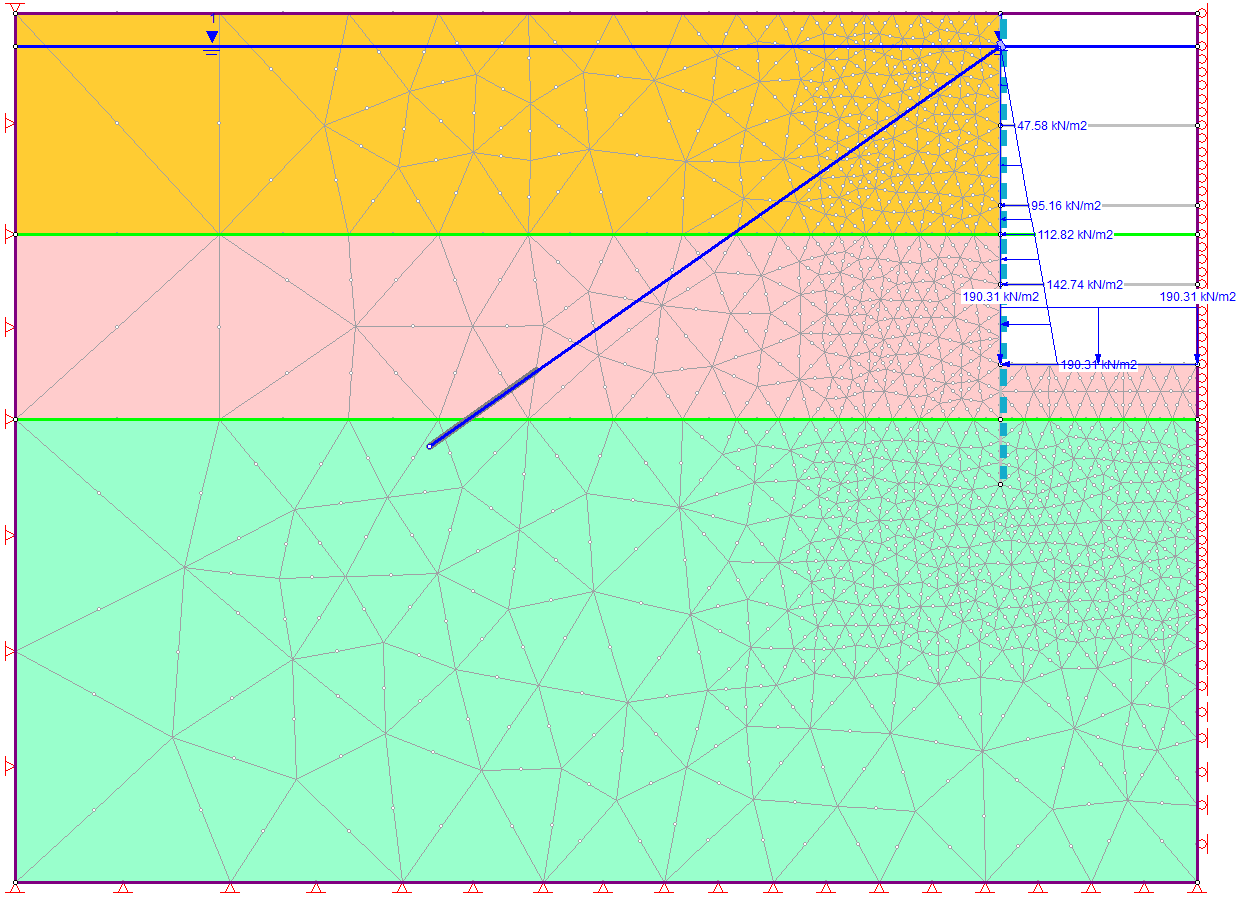
The material properties of the three layers of sands for the Hardening Soil are presented in Table 1. The strength characteristics, including friction angle, cohesion and tensile strength, are also the same for the two models.
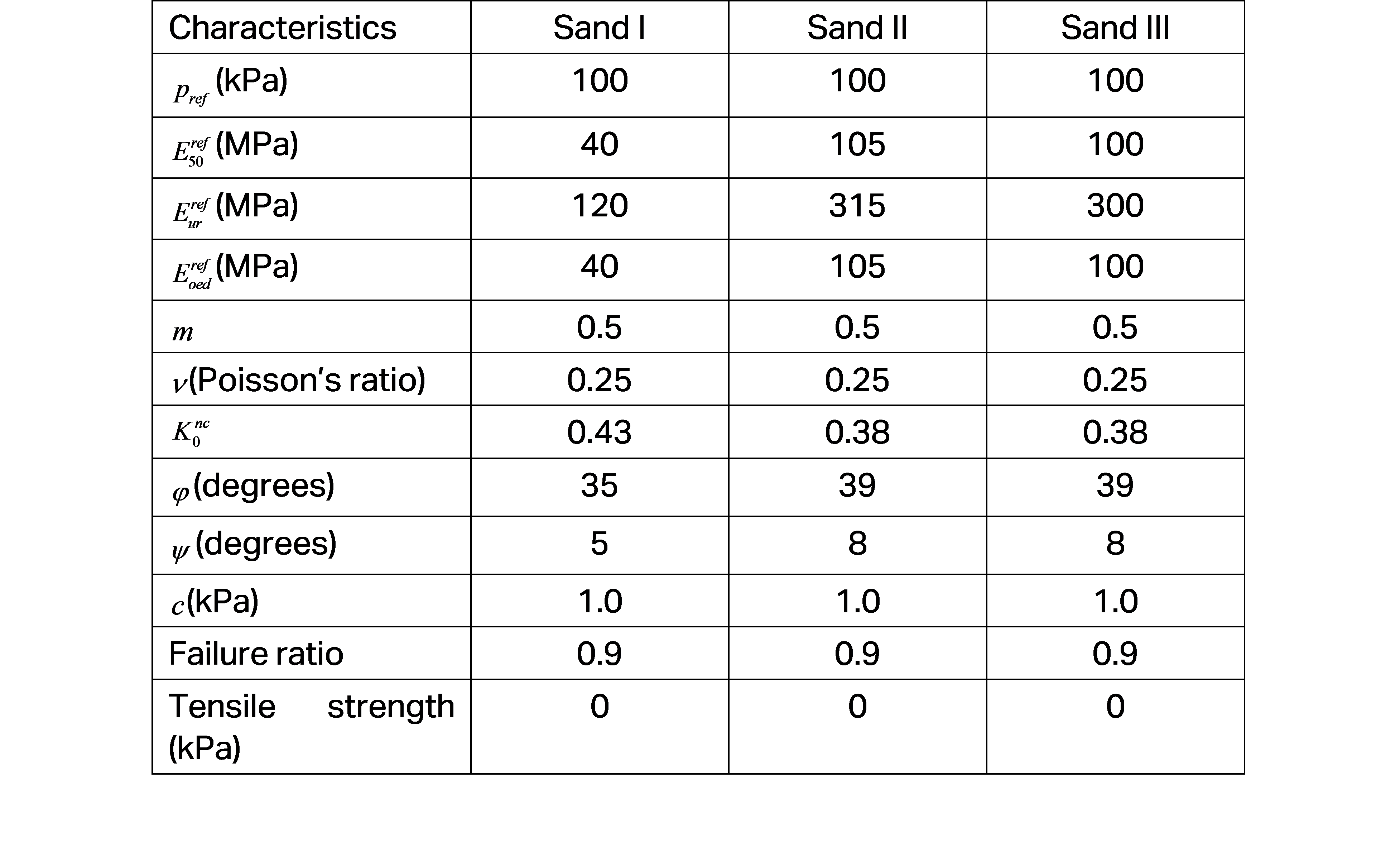

Results and Discussions
The horizontal displacement of the diaphragm wall was measured after the bolt installation and after the final stage of excavation. The following compares the simulation from the RS2 Hardening Soil model (RS2 HS) with the Plaxis Hardening Soil model (Plaxis HS) reported by Nikolinakou et. al. 2011 and the observed behavior.
In the first case, after installing the bolt, Plaxis and RS2 models are identical for the case of Hardening Soil model but both give lower bound estimation compared to the measurement.
In the second case, after the final excavation, Plaxis and RS2 Hardening Soil models are identical and both predict better results than in the previous case. Both models predict higher values of displacement at the bottom of the wall, but again, the predicted results are similar to the observed behavior.
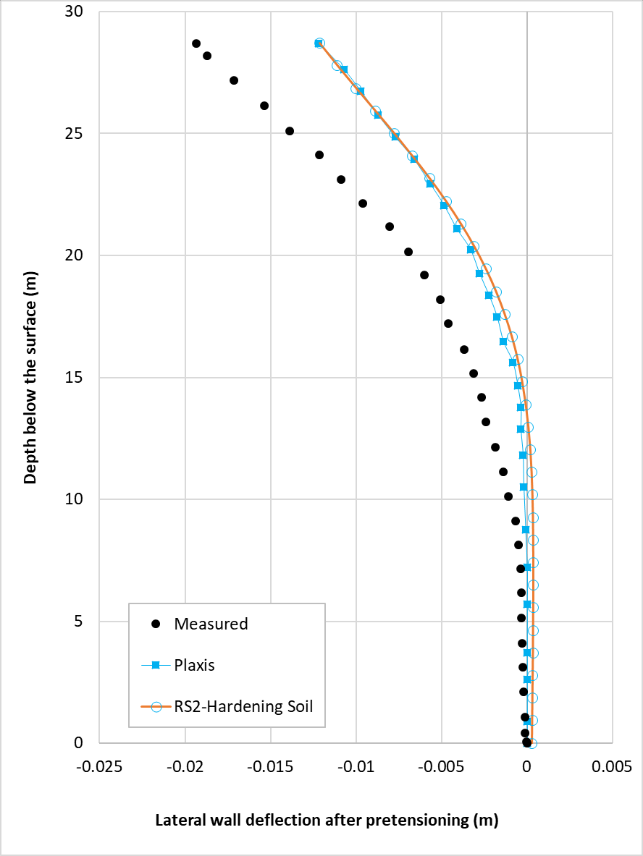
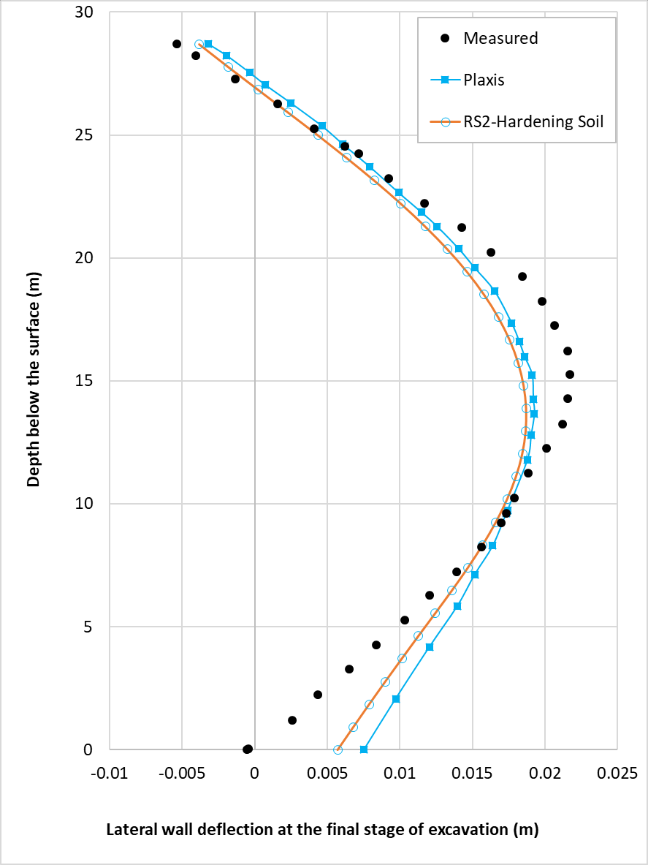
Conclusion
This article serves as an example of successful finite element simulations of geotechnical problems in soils. The focus was to select constitutive models that are more representative of the behavior of soils in the problem and carry out a finite element simulation that provides accurate predictions. Through modelling the deep excavation in Berlin sand, it has been shown that the Hardening Soil model provides reliable prediction for the behavior of sands. In the formulations of this material model, the salient features of the behavior of soils are considered and thus they can provide reliable predictions in finite element simulations.
References
Nikolinakou, M. A., Whittle, A. J., Savidis, S., & Schran, U. (2011). Prediction and Interpretation of the Performance of a Deep Excavation in Berlin Sand. Journal of Geotechnical and Geoenvironmental Engineering, 1047-1048.
Pietruszczak, S. (2010). Fundamentals of Plasticity in Geomechanics. CRC Press.
Azami, A., Yacoub, T., Curran, J., A practical constitutive model for sands (2015). 68th Canadian Geotechnical Conference, GéoQuébec 2015.