Finite Element Analysis Shootout: RS2 vs Plaxis vs DIANA
When it comes to selecting the right geotechnical software, functionality and precision are key factors. With the increasing complexity of problems, it’s imperative that the chosen software can generate results and ensure that those results are accurate and reliable.
This article looks at a thesis paper done by D.J. Kunst, comparing two geotechnical software programs which use Finite Element Analysis (FEA), Plaxis and DIANA. To compare their functionality and accuracy, a model for tunnel construction was created using a Tunnel Boring Machine (TBM). This testing was looking specifically at ground lining interaction.
Although both the software mentioned above use FEA, it should be noted that not all Finite Element Methods (FEM) work the same way and can sometimes approach the problem differently to compute the result. So a question from the thesis was; will these differences in software affect the results from the tunnel construction model?
Introducing RS2 to the mix
We wanted to include our software, RS2, to the comparison as well. Therefore, we put RS2 through the exact same tunnel construction testing model as Plaxis and DIANA.
Design of the Modelling
We will be focusing on the first 4 models described in the thesis. Each model calculation gets increasingly more complex.
Model 1- One soil layer and ring composed of one segment. Using Mohr-Coulomb and linear-elastic material models. Complete bonding is assumed for the soil-lining interaction.
Model 2- Soil layers changes from one to eight. These soil layers all have Mohr-Coulomb as constitutive model.
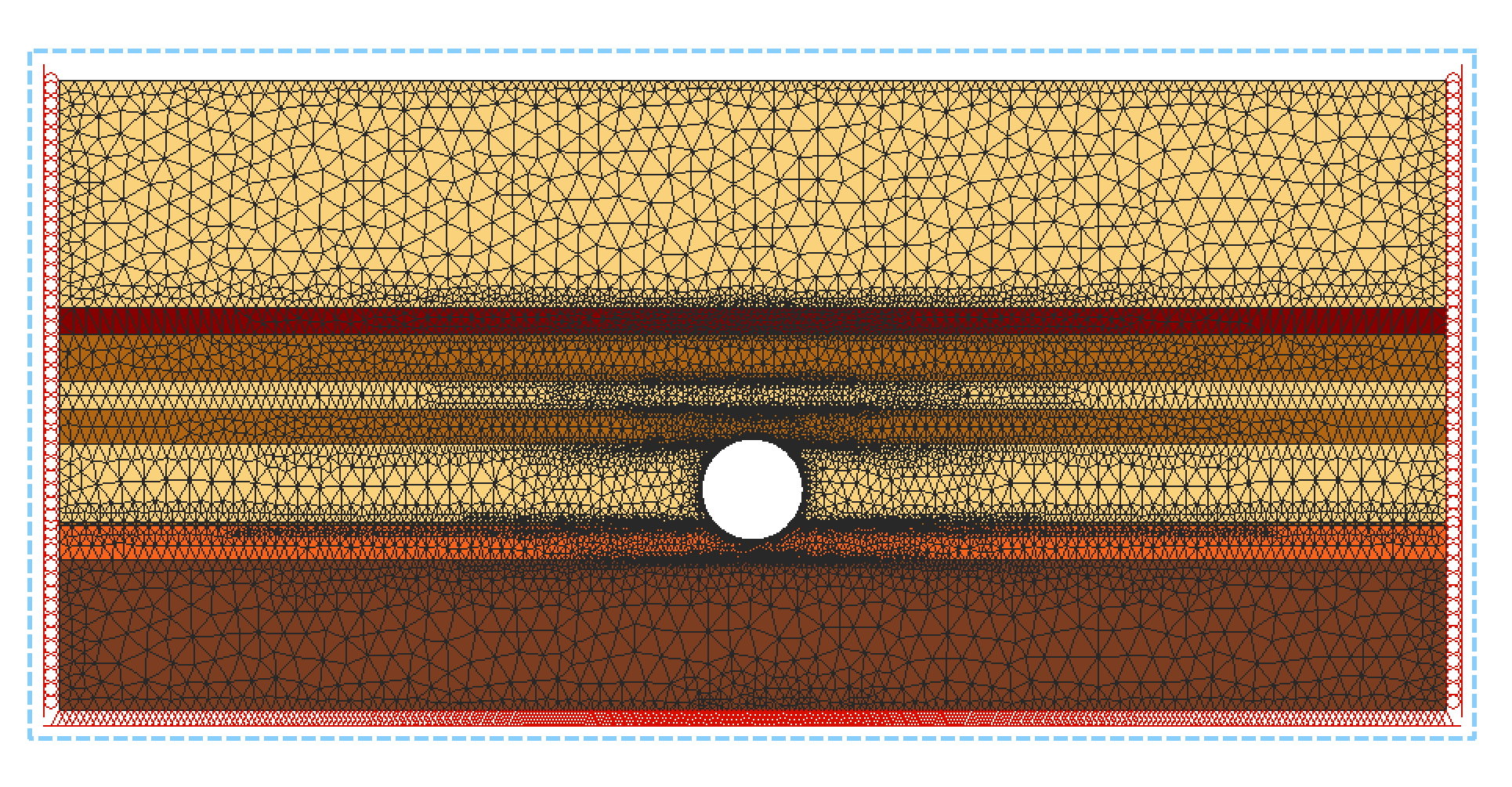
Model 3- Introduces slip bonding, reduction factor of 0.5 to account for partial slipping of the soil along the tunnel surface.
Model 4- Material Model of the soil changed to Hardening Soil Model in Plaxis and Modified Mohr-Coulomb in DIANA.
All 4 models have two stages:
1) The initialization phase, before the tunnel is installed.
2) The final phase, where the tunnel is in place.
Results from Testing Models 1-4
Model 1 results show that RS2 values in both Bending Moment and Axial Force are in agreement with the results from Plaxis and DIANA. When comparing these results to the calculations using Möller and Vermeer and COB-L500 methods, RS2’s data for Bending Moment is more precise than either Plaxis or DIANA.
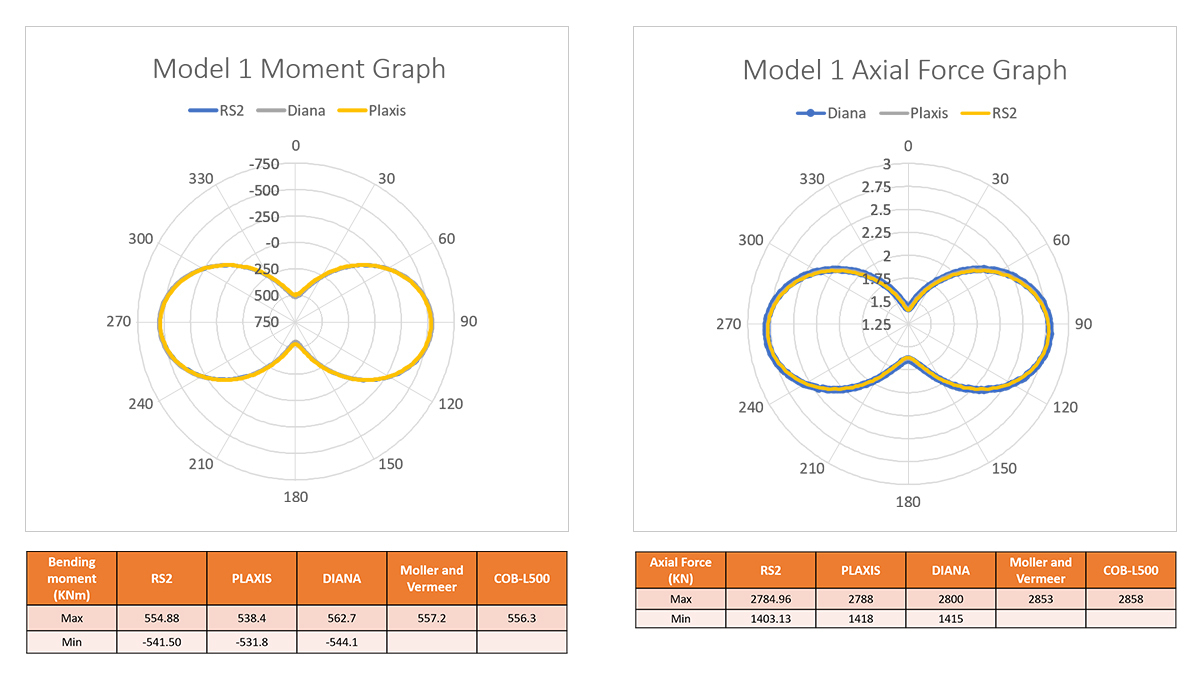
Model 2 results show RS2 calculations in both Bending Moment and Axial Force are consistent with the results generated by both Plaxis & DIANA.
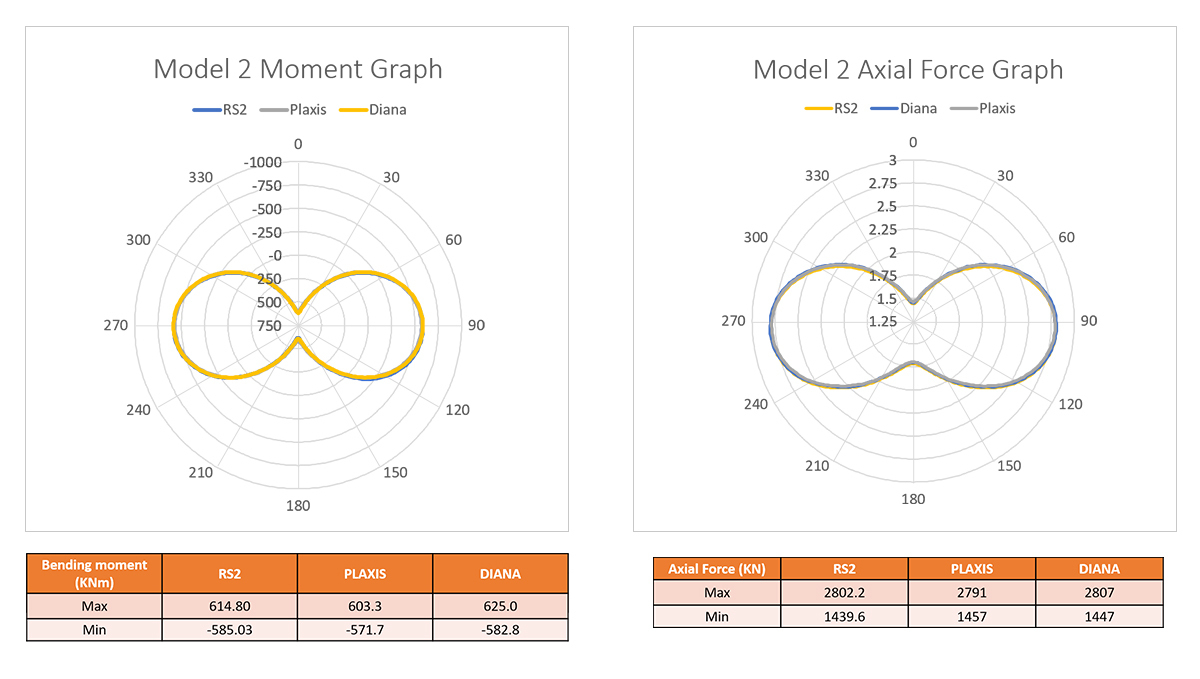
Model 3 results show that again, RS2 generated the same results as the other two programs. It is to be noted that in the Model 3 Axial Force Graph, the reason for RS2 dips can be attributed to RS2 giving a better graded mesh which caught additional axial forces that both Plaxis and DIANA missed.
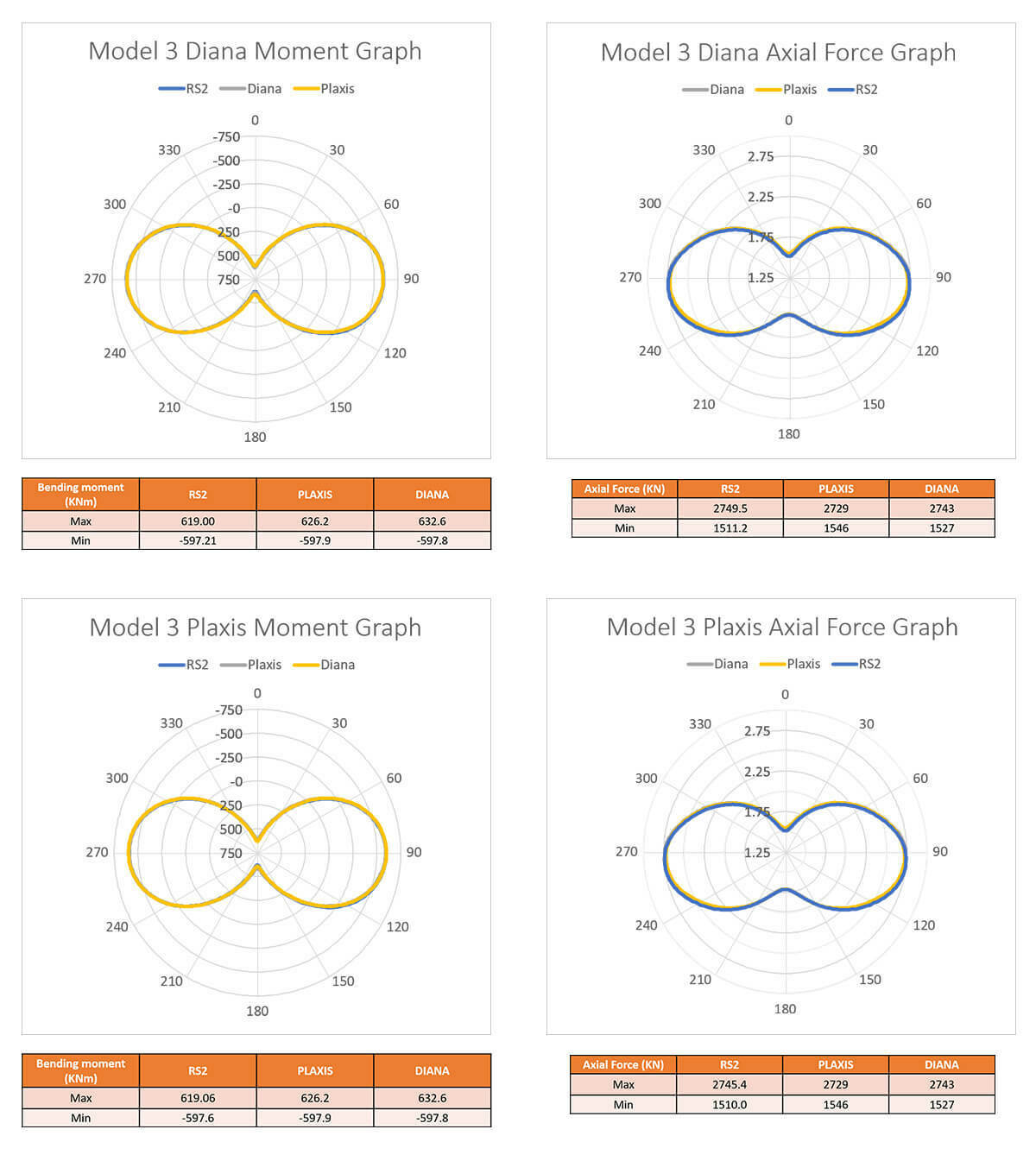
Model 4 shows RS2 results are consistent with Plaxis and DIANA. When looking at the results of the moment graph specifically, RS2 data is in between Plaxis and DIANA.
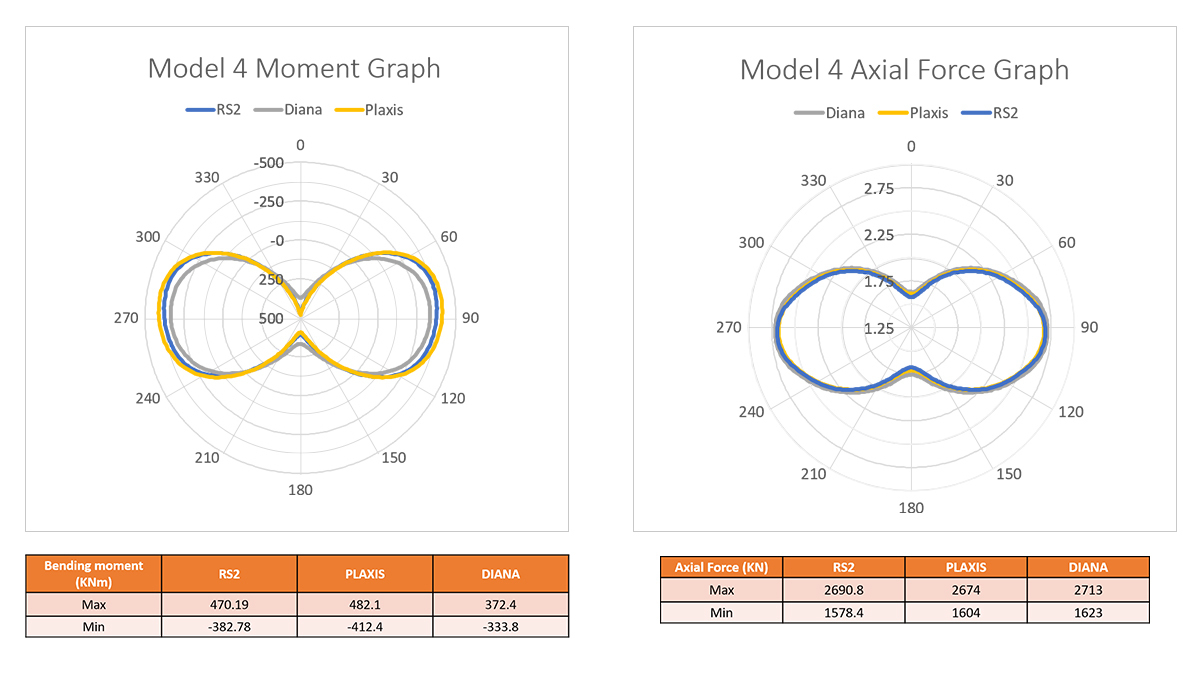
In Conclusion
After putting RS2 to the test in the same model of tunnel construction as Plaxis and DIANA, the results speak for themselves. The Finite Element Analysis from RS2 generated consistent and accurate results.
There are many factors to consider when choosing the right software. When functionality and accuracy are comparable across programs, the question becomes: which software will be the best fit for the analysis?