Useful, Practical Modelling of Underground Excavations with EX3
Introduction
EX3, the recently released overhaul of the Rocscience program, Examine3D, can be used to analyze and design underground excavations for civil engineering and mining applications. It is well suited to practicing geotechnical engineers and engineering geologists who need easy-to-use yet sufficiently powerful tools to model underground excavations. It is equally useful for heavy-duty numerical modelling.
Many geotechnical practitioners are competent in the discipline and possess several essential skills, including a firm understanding of the physical behaviour of geological materials. What many of them do not have is highly specialized numerical modelling skills. Practicing geotechnical engineers are also typically constrained by tight project timelines and limited budgets and thus need to develop reasonable solutions in a short time.
The article outlines what practicing engineers and engineering geologists, who are merely interested in solving their every day underground geotechnical problems, can do with EX3.
Modelling with EX3
The purpose of all numerical modelling in rock engineering is to evaluate the stress-deformation behaviour of rock masses and geological structures under excavation and other loading conditions. EX3 is a numerical modelling software based on the boundary element method (BEM). As the name suggests, the boundary element method (BEM) ‘discretizes’ (or divides into elements) the boundaries in a problem domain. Boundaries include geometric entities such as excavation surfaces, discontinuities, and material interfaces, for multi-material problems.
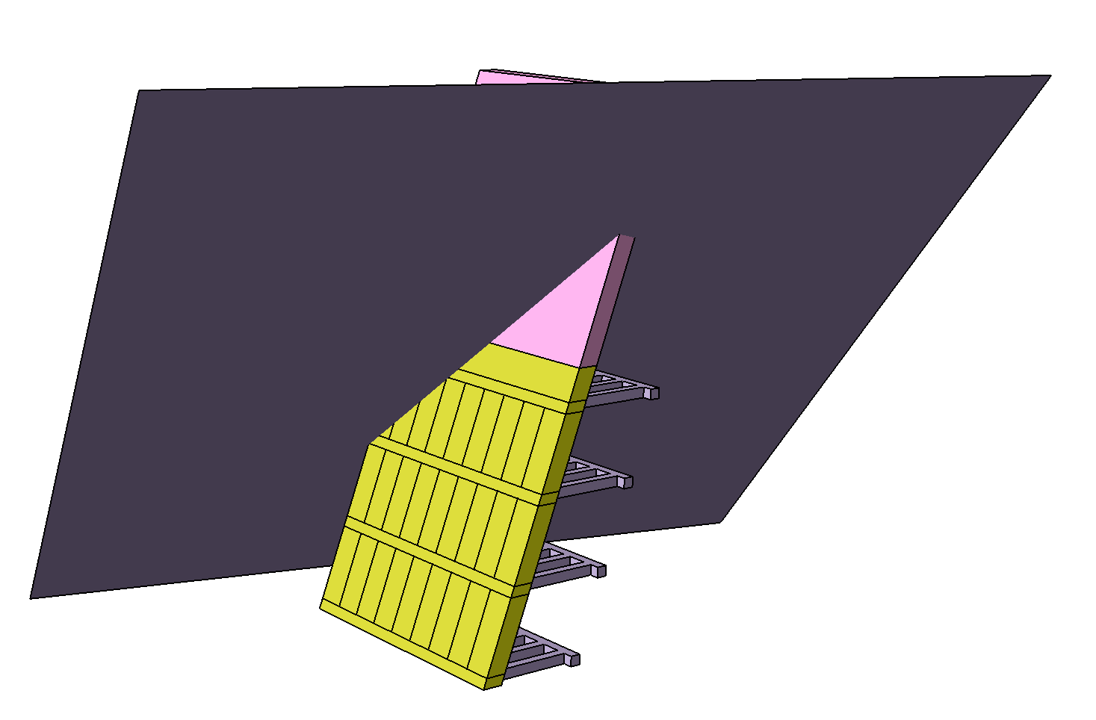
For linear elastic, homogeneous material problems, the BEM offers a key advantage of correctly modelling far-field boundary conditions, and confining discretization errors to problem boundaries. Because the BEM discretizes only boundaries, the sizes of its models are relatively small and compute fast.
Inputs required for numerical analysis of underground excavations include the following:
- In situ stress states (principal stress magnitudes and orientation)
- Excavation geometry, layout, and sequence
- Strength and deformation characteristics of rock mass units, faults, and other large-scale geological structures
- Strength, deformation, and mode of action of support systems or elements, and interactions between support and surrounding ground
- Location and orientation of faults relative to excavations (whether they daylight/intersect or are situated close to excavations), and
- Water pressures
EX3 takes all the above into account except for pore pressures and support (other than backfill). For support design, however, it can generate useful knowledge for estimating the lengths and capacity of support elements.
Modelling of effects of faults and other major geological structures on underground excavations
It is not uncommon for orebodies to be associated with geological features such as faults, shear zones, and intrusions. Civil engineering infrastructure such as power caverns and tunnels also regularly encounter major geological structures. These structures affect the stability of excavations. Modelling of the interactions between excavations and geological structures, particularly at mine-wide scales, is an essential area in the geomechanics of underground excavations.
Slip and separation of geological structures, which daylight into excavations, increase stress relaxation. In mining, for example, intersecting faults increase relaxation in hanging walls, allowing the formation of gravity-induced failures and significantly influencing ore dilution. Faults can also act as free surfaces that participate in the creation of rock wedges.
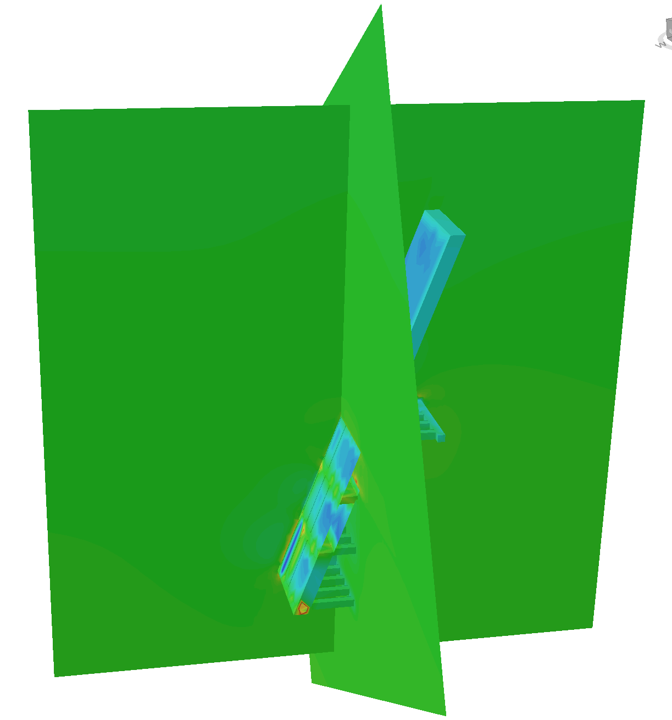
When a fault does not intersect but lies close to an excavation, slip along the fault can concentrate stresses in the rock mass volume between the excavation and the fault. In high-stress environments, this stress concentration can lead to rockbursts.
Differences in strength and deformation characteristics between fault materials and adjacent rock mass units also impact the distribution of stresses and displacements. This influences the degree of instability around underground openings.
EX3 can efficiently model the above-described excavation-fault interactions. Based on the outcomes, problem zones identified by EX3 can be further analyzed using programs such as RS3 and Unwedge. To facilitate practical modelling of underground excavations, EX3 can seamlessly import RS3 models, and RS3 can do the same with EX3 models.
Combining EX3 Elastic Analysis with Empirical Failure Criteria
Experience has shown that elastic stress-strain analyses, such as those that can be performed with EX3, can be combined with appropriate empirical failure criteria to make sound engineering judgement on the locations of problem zones.
As an example, rock mass zones around excavations and in pillars in high in situ stress environments, which experience varying degrees of damage, can be identified using empirical criteria based on deviatoric stress. (Deviatoric stress is defined as
σ1-σ3
where σ1 and σ3 are the major and minor induced principal stresses, respectively.)
For typical hard rocks, experience shows that damage is initiated when the ratio of deviatoric stress to laboratory uniaxial compressive strength of intact rock, sometimes termed the brittle shear ratio (BSR), attains values between 0.3 and 0.4.
BSR = (σ1-σ3) / UCSintact
The BSR criterion is a useful indicator of different degrees of rock mass instability associated with high induced deviatoric stresses. Table 1 below (Castro et al.) provides an example of empirically established rock damage levels based on BSR. Engineers can develop similar tables for their specific underground settings based on observed damage.
Table 1. Levels of rock mass damage based on BSR.
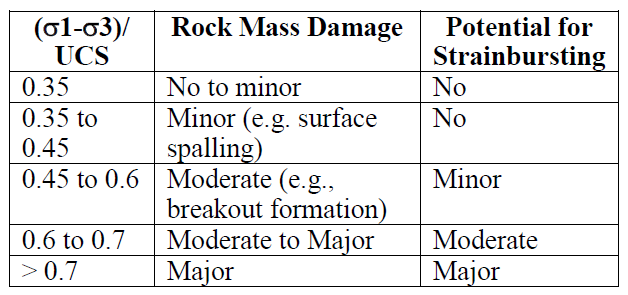
The BSR criterion does not account for rock mass deformability. As a result, it does not sufficiently capture the energy release potential of highly stressed rock mass volumes. Energy release rate (ERR) is an energy-based criterion commonly used to account for energy release potential. Work is going on to implement ERR in EX3 to allow practitioners to gain further insights into bursting potential.
Concluding Remarks
Engineers can gain a considerable understanding of the behaviour of rock masses and major geological structures due to excavation (both mining and civil) using the relatively simple analysis tools provided in EX3. The combination of speed and simplicity makes EX3 ideal for practitioners and researchers alike. They can use the tool to model the following:
- Stability of excavations, including mining haulage networks (drifts and crosscuts), under a variety of conditions
- Stress redistribution induced by the excavation of mining stopes
- Effects of different stope sequences, allowing engineers to use stope sequencing to control induced stresses in ways that minimize geomechanical problems.
- Stress-deformation interactions between excavations and major geological structures
- EX3 provides reasonable first estimates of the extents of de-stressed zones (which can then guide support design and highly stressed zones at risk of bursting and requiring preconditioning)
- EX3 can also help delineate zones of dangerously high stress concentrations that can lead to rockbursts, and
- Potential pillar problems (for example, high induced stresses that lead to bursting) and evaluate different strategies and tactics (such as support systems) for minimizing adverse impacts of stress redistribution from excavations.
Modelling with EX3 can help engineers and engineering geologists gain valuable insights into potential failure modes, rock mass areas in which they are likely to occur. Practitioners and researchers can use these tools to develop design solutions, rationally compare alternatives, and identify those that require more detailed analysis. EX3 helps practitioners to optimize the use of critically limited resources such as time and budget. It is particularly useful for undertaking parametric and sensitivity analyses that help engineers identify the uncertainty and risks in their design choices.
EX3 can give surprisingly useful engineering insights despite its simplicity.
Reference
Castro LAM, Bewick RP, Carter TG. 2012. An overview of numerical modelling applied to deep mining. In: Azevedo R, editor. Innovative numerical modelling in geomechanics. London: CRC Press; 2012. p. 393-414.