Developing New Formulas for Room and Pillar Mining Design With RS2 and RS3
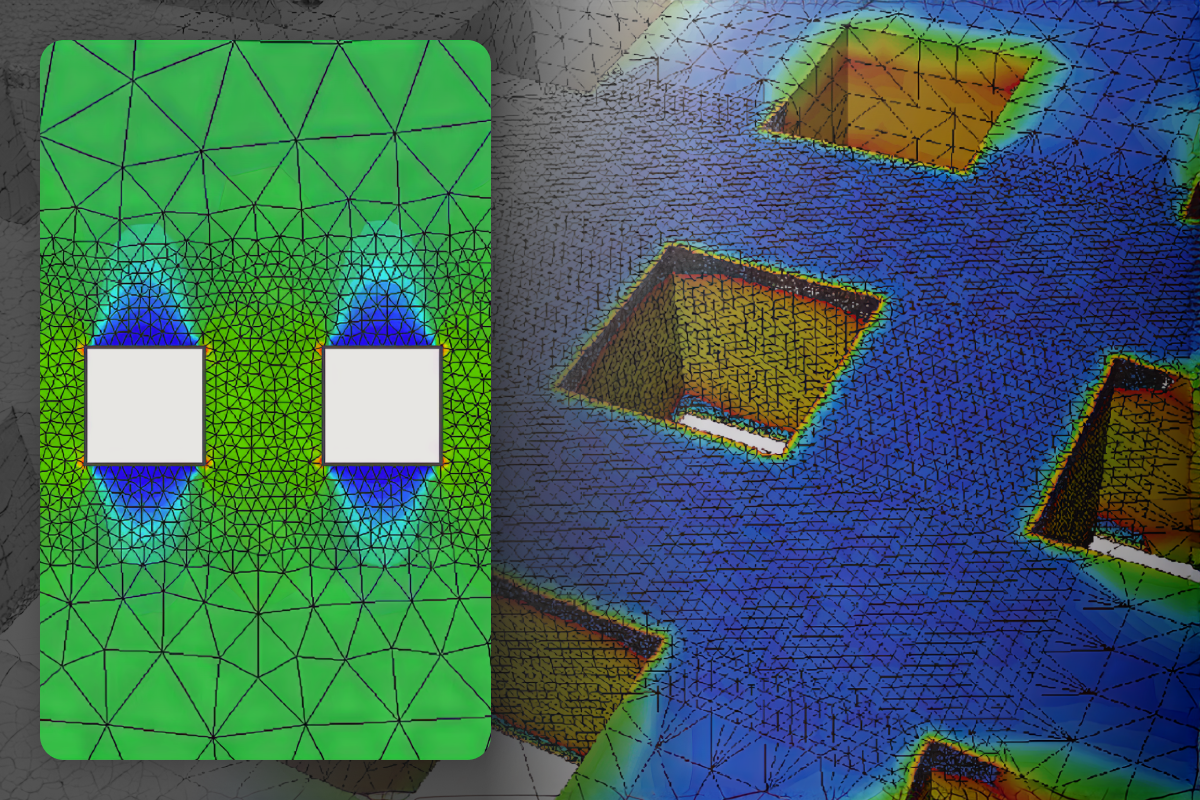
What if the traditional methods we rely on to ensure the safety of underground mining operations could lead to inefficiency and risk? These errors in predicting stress on mining pillars can result in either costly overengineering, or worse, catastrophic failures.
Researchers from the National Technical University of Athens turned to RS2 and RS3, our 2D and 3D finite element analysis software, for a solution that could more accurately predict stress than Tributary Area Theory (TAT).
Here we’ll cover how RS2 and RS3 were used in the research to develop new pillar design formulas that can improve safety and operational efficiency, and for the full insights, read Ioannis Vlachogiannis and Andreas Benardos’ paper here.
The Backstory
Pillars are designed to support overburdens while maximizing resource extraction. Historically, tributary area theory (TAT) has been the go-to method for estimating pillar stresses in room-and-pillar mining. But it frequently overestimates stresses by ignoring complex stress redistribution mechanisms, which can lead to larger-than-necessary pillars that reduce mining efficiency and increase costs.
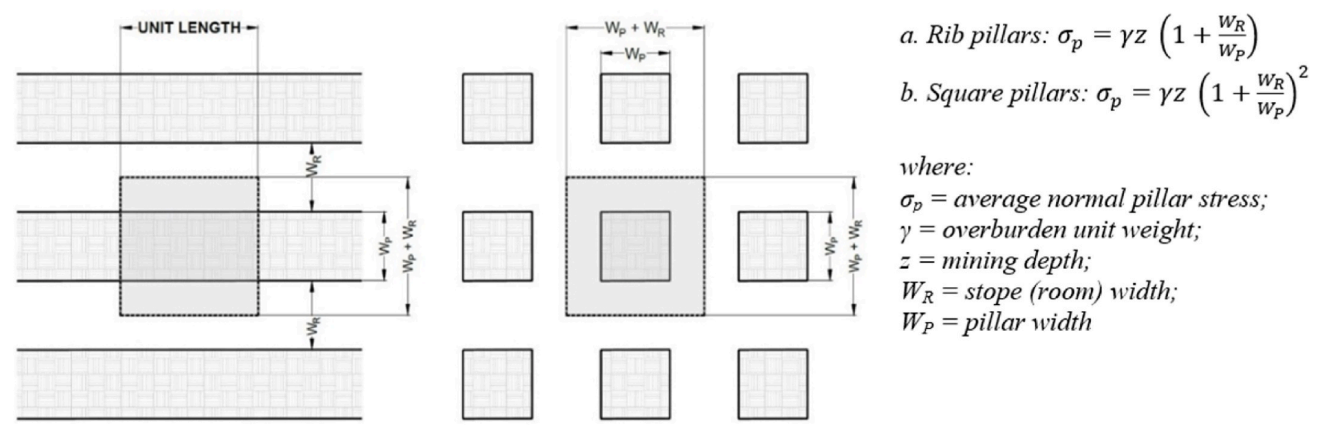
The Challenge
The research team aimed to overcome the limitations of the Tributary Area Theory (TAT) in predicting pillar stress, especially when considering the complexity of different pillar geometries. To achieve this, they needed to employ both 2D and 3D finite element analyses to model stress distributions in rib and square pillars.
Simulating and analyzing this broad range of pillar configurations was the goal, and the challenge lied in creating new formulas and validating they could outperform TAT and be applicable across diverse mining scenarios.
The Solution
RS2 and RS3 offered the advanced finite element analysis capabilities necessary to accurately model stress in room-and-pillar mining. These tools enabled detailed analysis of the complex geometries of different pillar types, and each addressed specific aspects of the stress modeling process.
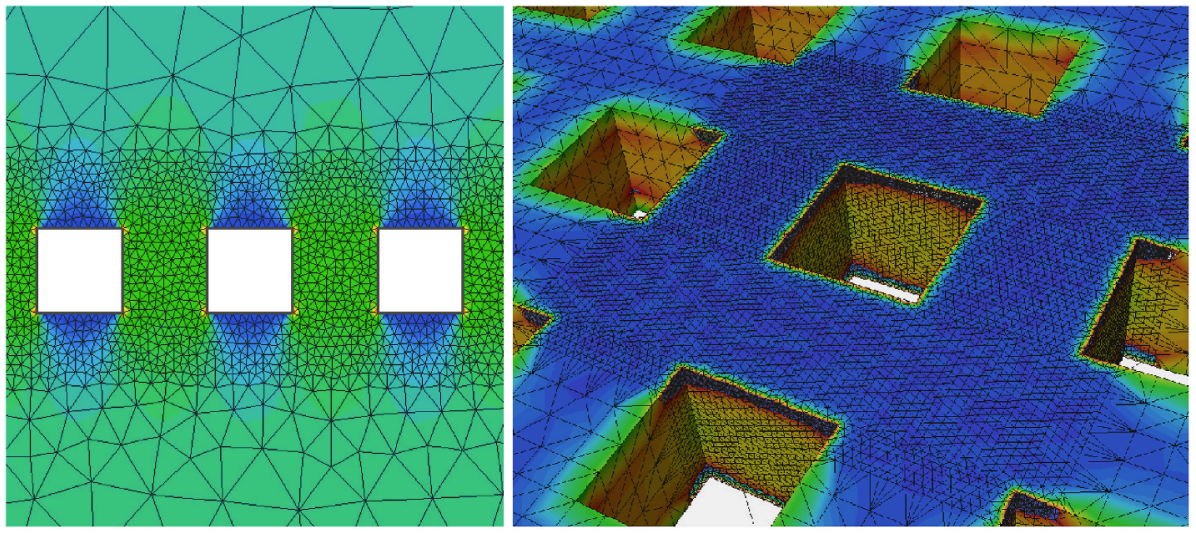
2D FEA With RS2
The team used RS2 for 2D finite element analysis, focusing on rib pillars with a high length-to-width ratio (Lp/Wp > 10), where plane strain conditions are critical. This setup allowed for accurate simulation of stress distribution along these long, narrow pillars.
The team was able to precisely estimate the vertical stresses anticipated within these rib pillars where traditional methods would fall short. The 2D FEA captured the stress distribution along the length of the pillars and provided detailed insights into how these structures would perform under various loads and depths.
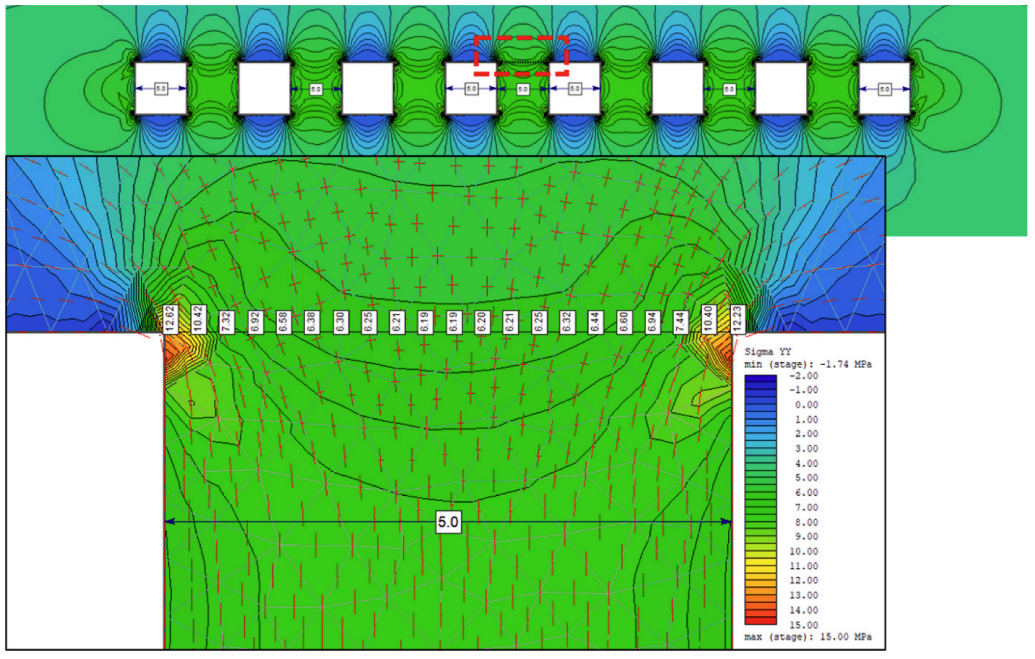
3D FEA With RS3
To address the limitations of 2D analysis and model the full complexity of room-and-pillar layouts, the researchers employed RS3 for 3D finite element analysis. This was particularly important for square pillars, where cross-cutting stresses play a significant role.
RS3 enabled a comprehensive stress analysis that accurately represented the interactions between pillars and surrounding rock. These 3D simulations were instrumental in capturing stress concentrations at pillar edges and corners that are typically prone to overstressing and failure. Correlating these 3D results with the 2D analyses ensured consistency and validated the new stress estimation formulas.
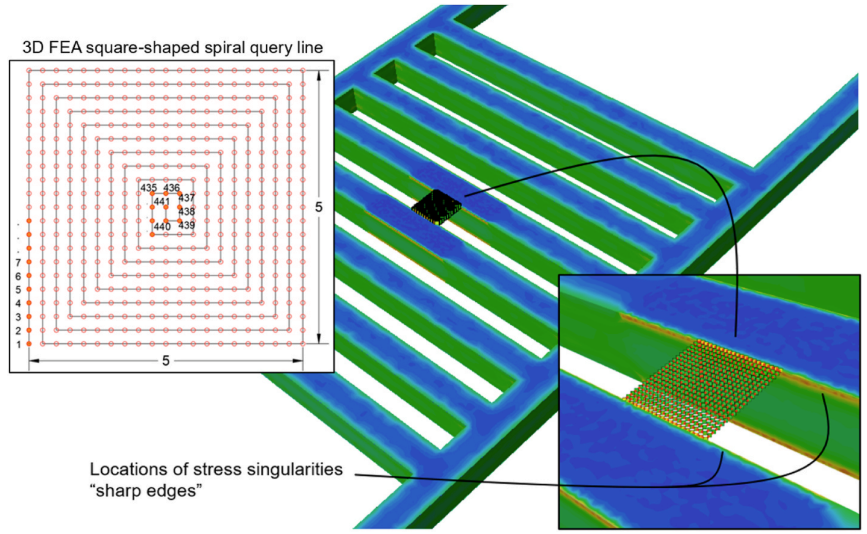
The Results
By combining 2D and 3D FEA, researchers overcame the limitations of traditional methods and developed new, reliable formulas that accurately reflect the complexities of pillar stress in various mining conditions. Overall key findings from the study include:
A More Accurate Method of Stress Estimation: The new formulas closely matched FEA results, with deviations of less than 5% for rib pillars and under 2% for square pillars. This high level of accuracy shows their reliability for real-world mining applications.
TAT’s Overestimation Was Confirmed: The study revealed that Tributary Area Theory (TAT) overestimates pillar stress, particularly in slender square pillars, by up to 2.5 times. TAT fails to account for complex stress redistributions and interactions between pillars and surrounding rock, which leads to overly conservative designs. The newly developed formulas overcome this by providing more accurate and realistic stress predictions that better reflect the actual mine conditions.
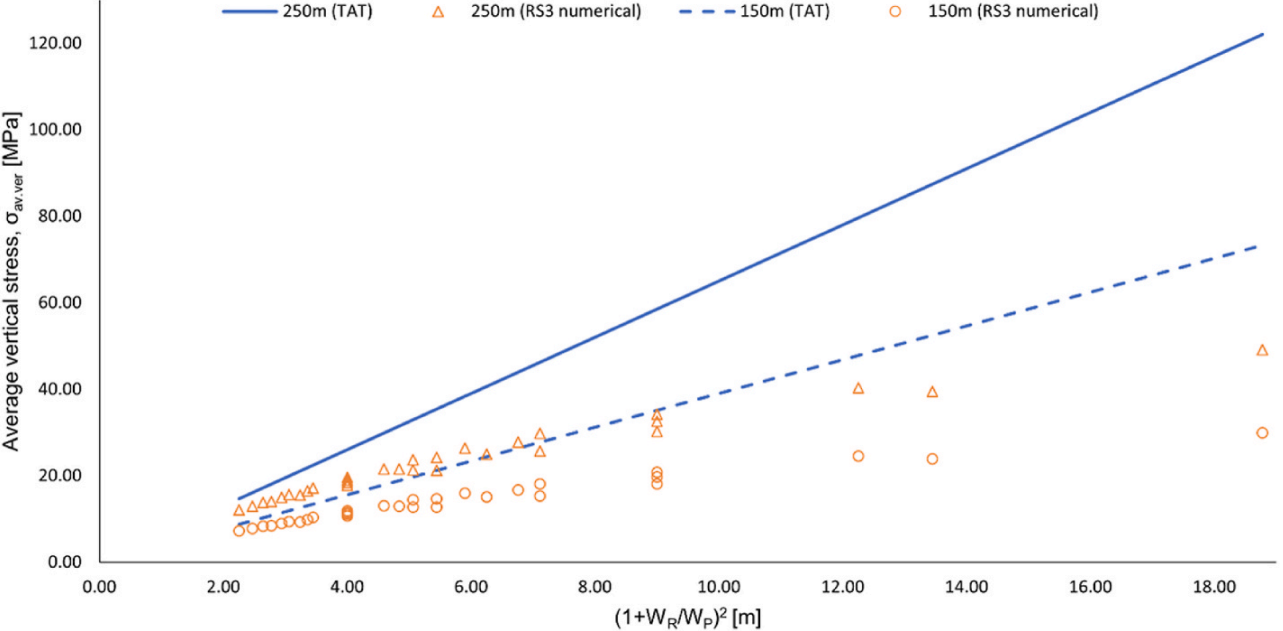
The Formulas are Versatile and Efficient: Validated across a range of overburden depths (50 m to 350 m), these formulas are applicable to various mining conditions. Their efficient computational development also supports practical implementation, so both the design and operational phases can have time and cost savings.
Additionally, the newly developed formulas are:
For Rib Pillars:
σav.ver = S𝑣 x (1+WR / WP) 0.8
Where:
- σav.ver is the average vertical stress on the rib pillar crest.
- 𝑆𝑣 is the geostatic stress (the stress due to the weight of the overburden).
- 𝑊𝑅 is the room width.
- 𝑊𝑃 is the pillar width.
For Square Pillars:
σav.ver = 2.1 x S𝑣 x WR0.9 / WP0.7
Where:
- σav.ver is the average vertical stress acting along the rib pillar crest.
- 𝑆𝑣 is the geostatic stress.
- 𝑊𝑅 is the room width.
- 𝑊𝑃 is the pillar width.
The Verdict
RS2 and RS3 demonstrated the effectiveness of advanced finite element analysis in developing and validating more precise stress estimation formulas. With these tools, engineers can more reliably optimize resource extraction and design safer mining operations.
Frequently Asked Questions About Room and Pillar Mining Design
Why is Accurate Stress Prediction Important in Room and Pillar Mining?
Getting an accurate stress prediction directly impacts the safety and stability of the underground structures. Pillars need to withstand the specific loads they will encounter, but the design also needs to be aligned with the overall scope and budget of the project.
Incorrect stress estimates can lead to overengineered pillars, wasted resources, or under-designed pillars, all of which risk collapse and could harm anyone in the mine.
What are the Typical Challenges in Designing Safe and Efficient Mining Pillars?
There are several possible challenges, including accurately predicting stress distributions, accounting for varying geological conditions, and balancing material use with stability requirements. Engineers must ensure that pillars are strong enough to support the overburden without being overly conservative, which would waste resources.
Additionally, the complexity of pillar geometry and the need to consider different mining depths and configurations make the design process intricate and demanding. But tools like RS2 and RS3 can help!
How Does Overburden Pressure Affect Pillar Stability in Room and Pillar Mining?
Overburden pressure, meaning the weight of the rock and soil above the mining pillars, impacts pillar stability because higher overburden pressures increase the stress on pillars, requiring more robust designs to prevent collapse.
Inadequate consideration of overburden pressure can result in pillar failure, leading to potential safety hazards and operational disruptions. Engineers should properly account for overburden pressure to design pillars that can safely support the load above them.
What are the Limitations of the Tributary Area Theory (TAT) in Pillar Design?
The Tributary Area Theory (TAT) limitations are in its tendency to overestimate stress, especially in complex geometries like slender square pillars. TAT assumes uniform load distribution and doesn’t account for the intricate stress redistributions that occur in actual mining conditions. This often leads to overly conservative designs that do not optimize material use or fully account for the real stress environment, so it can be less reliable for modern mining operations.
What are the Benefits of Using Finite Element Analysis (FEA) in Mining Design?
Finite element analysis (FEA) offers numerous benefits in mining design, including enhanced accuracy, detailed modeling, and the ability to simulate complex stress conditions. FEA allows engineers to create precise models of how stress is distributed across various pillar geometries and materials, leading to better-informed design decisions. This level of detail helps in optimizing pillar size and layout, improving both safety and efficiency while reducing the risk of overengineering or structural failure.
How Do 2D and 3D Finite Element Analyses Together Improve Pillar Stress Estimation?
2D and 3D finite element analyses (FEA) can provide you with detailed, accurate models of stress distribution within pillars to significantly enhance pillar stress estimation. Unlike traditional methods, FEA accounts for the complexities of pillar geometry and material properties, which offers a more precise simulation of stress distribution across different configurations.
By modeling both 2D and full 3D conditions, FEA provides a comprehensive understanding of your potential stress points to help you make better-informed design decisions.